Overview
The Moulding and Tooling Divisions of the business fall within the scope of our ISO9001:2015 quality management system.
A robust and fluid quality system has been developed to cater to specific customer quality requirements, these are controlled and monitored through internal and external audits. There is an ethos of continuous improvement in all areas of the business and the team is focused on controlling the process of the products that we provide whilst always looking to see what improvements can be made.
The quality department are involved from a very early stage for new products and repeat production providing First Article Inspection Reports (FAIR) at the initial sampling stage and in-process controls for repeat production runs. All parts have an individual quality plan, setting record, part code history, bill of material and routing operations to ensure every stage of manufacture is completed in a controlled manner.
What quality support can Pentagon provide?
• ISO9001:2015 certificate
• Fully controlled quality management system
• Internal audits to maintain procedures and process
• Bespoke quality plan documents for all products
• Dimensional, visual and functional review of components
• Documented records of process checks
• First Article Inspection Reports & PPAP Level 3
What equipment supports the process?
• A range of CMM technology
• Shadowgraphs
• Standard micrometers and calipers
• Gauges – thread, plug and ring
• Mating parts for fit or function
• Calibrated equipment to standards
A full management system review is conducted annually with weekly quality and improvements meetings to ensure the quality system is maintained, is relevant and can support the manufacturing process at every stage. The areas we monitor are concerns, issues, trends and improvement opportunities.
Suppliers are monitored for performance and action is taken to support them if they fall below the high standards we expect within our supply chain network.
QUALITY POLICY
The Pentagon Plastics Group, incorporating Pentagon Plastics Ltd and Pentagon Tooling Ltd, understand the importance of Customer Satisfaction at every stage of the services we provide. We strive to achieve a level of quality that will meet or exceed our customers’ expectations and comply to all customer, regulatory, and statutory requirements.
The assurance of quality is fundamental in all work undertaken and is backed up by complete traceability through the implemented systems.
The Quality Policy of the Company is to: –
Establish and maintain a Total Quality Management System (TQMS) which satisfies the requirements of ISO 9001:2015 and comply with customer specific quality requirements.
Consistently provide products and services that satisfy customer requirements in all respects.
Implement appropriate actions to address any risks and identify opportunities associated with both internal & external issues, and to meet the needs and expectations of interested parties.
Ensure all Company personnel are competent to carry out their assigned tasks and are fully aware of the TQMS including how to implement it in daily tasks.
Strive to continually improve our services provided to customers, using our policies, quality objectives, and performance evaluation including results of audits, non-conformance, and management review.
Establish annual quality objectives at strategic and operational levels within the Company, that are measurable and reported upon at the management review.
Maintain documented information as objective evidence to demonstrate compliance with the TQMS.
Control & continually monitor all projects undertaken.
Comply as a minimum with all applicable statutory and regulatory requirements.
Review the TQMS system as a minimum annually to ensure it is effective, relevant, and delivers the quality standards that we strive to achieve.
The senior management team commits to the above statements and actively encourages its implementation by personnel at all levels of the Company. This Quality Policy is reviewed periodically by the senior management team while considering trends, root causes and opportunities for improvement as part of the drive to support continuous improvement ensuring that objectives are met.
By signing this document, the Director gives approval of the Quality Policy and supporting the Total Quality Management System described in the Manual (MAN01_MS) and all supporting company processes.
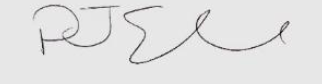
Paul Edwards