The Moulding Divisions at Pentagon is ISO9001:2015accredited, putting quality at the very heart of the manufacturing services provided by the group.
The injection moulding production process is controlled through a strict and robust quality regime. Lloyd Bolton, Quality Leader at Pentagon heads up the 4 strong team spanning both day and evening shifts. Lloyd’s product knowledge is second to none having been with the company since 2014.
Each year Pentagon sets Quality Objectives which are clearly communicated to all employees. These objectives are then tracked, reported, documented, and reviewed throughout the year to ensure set objectives are met and maintained.
Quality control at Pentagon begins the moment raw materials, inserts and all other purchased (and free issue) items enter Goods In. All goods received on site are thoroughly checked before being despatched to the relevant warehouse. The stringent quality checks then continue through every stage of manufacture including tool preparation and injection moulding.
Quality Inspectors undertake patrol checks for the operating machines, packing room and post moulding area every 1-2 hours. Taking samples and measurements, using equipment including CMM, Callipers, Micrometres, Height Gauges, Pin gauges, and custom-built customer-specific jigs and gauges.
Measurements are recorded against the part history database enabling production history to build and from this data the production team can see if overtime a particular part dimension has changed, allowing capture and reporting before it becomes an issue for the customer. The Post Moulding and Packing operators visually inspect product as they work with final inspection checks and final pallet checks performed by the Quality Inspectors.
For all production parts produced in the Moulding Division, two types of production samples are retained which consist of the customer-approved Gold Sample and previous production run samples. The production samples are used by the Quality Inspectors during First off and in-process checks for comparison to ensure high levels are maintained.
Waste tracking: non-conforming parts are accounted for on Waste Tracking forms in each area of Production. These forms are completed by the operators to highlight how many rejects and the type of rejects for each job. These are then reported back enabling the quality team to build up a picture of problem areas that are causing high reject rates and thus material wastage.
The group operates a bespoke Quality Service Concern (QSC) reporting feature, used for recording customer complaints, internal non-conformances and Supplier Issues used to ascertain root causes and any resulting corrective and preventative actions (CAPA). If a complaint originates from a specific area, then the Supervisor of that area is included in the investigation process to help with understanding of the issue and reduce the possibility of it happening again.
Quality Inspectors on both shifts provide daily reports for the Quality Leader, highlighting any issues like rejects, out of tolerance dimensions, additional checks performed. e.g., Final inspection checks. Quality Leader uses these daily reports to create weekly reports to Operations Director on things like; total parts through areas, reject percentage, reject DPPT (defective product per thousand), QSC status as a few examples.
The rigorous quality processes throughout the organisation makes quality everybody’s responsibility at Pentagon.
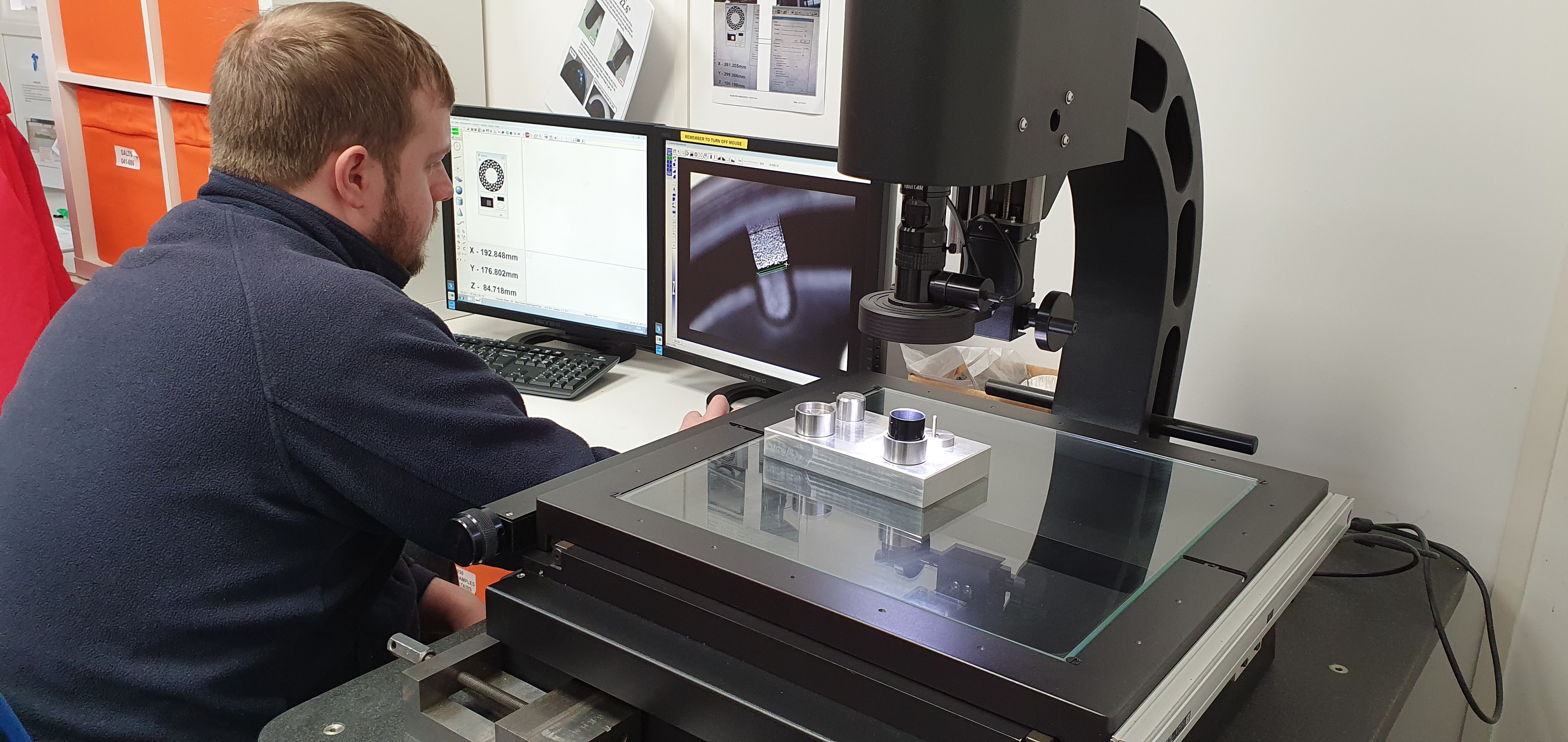